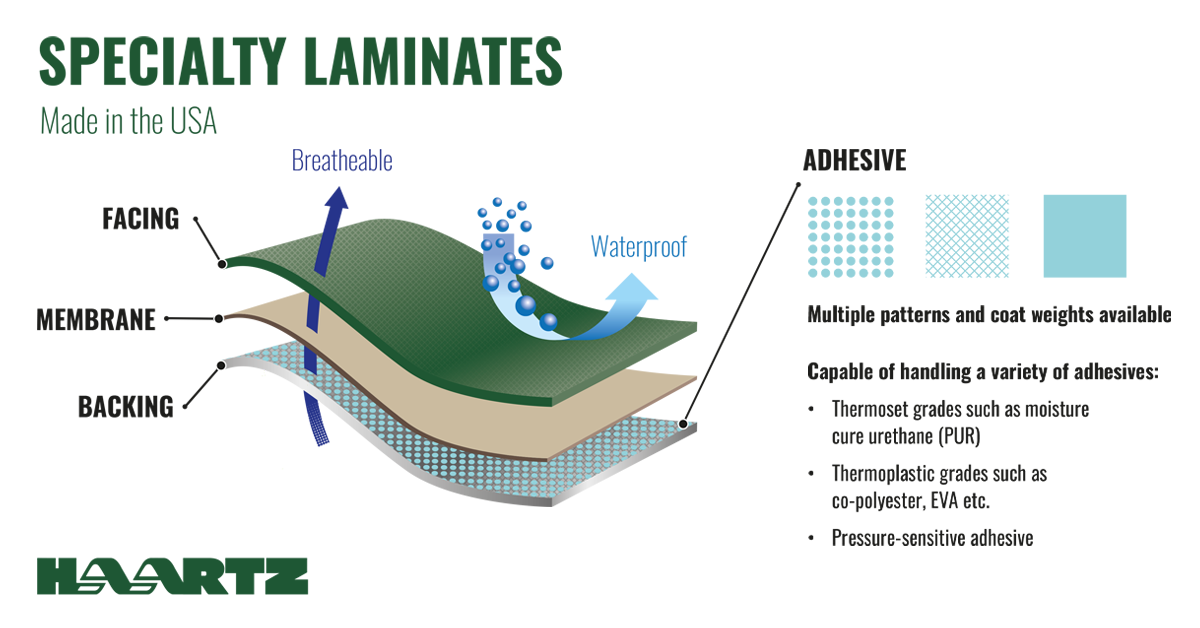
Specialty laminates are a class of textiles created by bonding or laminating multiple layers of fabric together to offer specific performance qualities or functional characteristics unachievable through the use of a single-layer material. The use of multiple layers allows specialty laminates to incorporate different properties throughout their design.
Functions vary but can include alterations to account for waterproofing, durability and resistance to environmental factors – making specialty lamination a widely used process throughout multiple industries. Apparel and footwear, marine fabrics, military and tactical gear and automotive interior materials are just a few different products that use specialty laminates.
These alterations improve overall functionality but also make materials more complicated. When determining the best type of material to use, there are several properties companies should consider depending on the purpose the final product is meant to serve.
Understanding the Basic Functional Properties
Since two or more layers are always used in specialty laminates, companies should ensure they understand the process and how the available options will enhance their final product.
Functional properties can include materials that excel in waterproofing, are wind-resistant and breathable, or provide flame resistance or electrostatic dissipative properties. Depending on its industry, a company should work with a manufacturer that can easily help identify what properties are best for their current market.
Manufacturers can further customize specialty laminates to meet precise needs by adjusting the adhesive formulation, adhesive laydown pattern, layer thicknesses, color and texture to increase performance. The layers used in specialty laminates can also be made from various materials like nylon, polyester and natural fibers, or even non-textile materials such as films, foams, or membranes.
There are also options for different methods of bonding layers, including adhesive bonding, or heat bonding. Ultimately, the choice of bonding method will depend on the specific requirements of the laminate, but a company must ensure they're working with material engineered for durability and longevity, especially if it's used in challenging environments or applications.
Lastly, a company will always need to factor in the cost of the job. The production of specialty laminates can be more complex and costly than single-layer fabrics, mainly due to the additional manufacturing processes involved, so a company will need to keep this in mind.
Does your company have questions and is looking to learn more? Turn to an expert like The Haartz Corporation. Over our more than 100 years of operations, we have invested in various adhesive capabilities from moisture cure urethane (PUR) and co-polyester to EVA and pressure-sensitive adhesive. Challenge us.