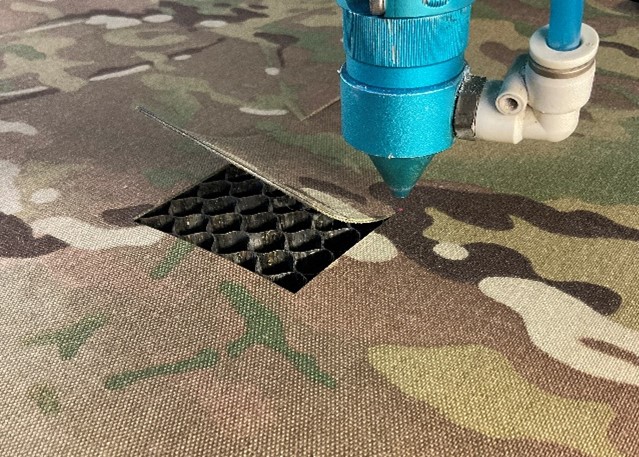
Author: Kory Brown - Alpen Design Works. Although once labeled as a passing trend and a novelty, laminates and laser cutting have certainly revolutionized everything from tactical gear to fashion. With the ever-increasing availability of affordable laser cutting systems, this technology is no longer limited to big brands but can be found in use by small businesses and hobbyists alike.
However, laser cutting nylon laminates can create a few challenges. Here are four tips to help improve your laser cutting:
#1 - Verify and utilize the correct focal length
Each laser and lens combination will have a slightly different focal length (the distance from the lens that the beam is at the most narrow point), and for best results, that measurement should be verified and maintained. Relying on factory settings for an auto-focus feature is not always reliable. Even a small amount of defocusing can cause the laser beam to have a much larger surface area, resulting in melting and discoloration around the cut path. For best results, conduct a ramp test and keep a physical gauge on hand that can be used to verify proper focus.
#2 - Optimize speed and power
The most common error we see is running a laser at maximum power to allow the fastest possible speed, under the pretense that will allow more cutting to be done in less time. Often, this results in poor quality cuts as the laser beam cuts through the material with excess energy, reflecting off the honeycomb surface below, leaving divots and discoloration on the underside of the material. Finding the right pairing of speed and power will give enough energy for a clean cut, without risking damage to the underside.
A tangential issue to this is seen when the settings are tested on small cuts, but not verified for longer cut lengths. During small cuts, the laser may not approach the higher end of the speed setting like it will on longer lengths, which may lead to sections where the cut is not complete. Be sure to test your settings with multiple types of cut lengths and shapes.
#3 - Prevent material curling
Laminates tend to have more severe roll memory than single layer fabrics, which can cause problems for laser cutting. While the material may lay flat coming off the roll, as parts are cut, the roll memory can cause them to lift off the cutting surface. This results in poor or incomplete cutting and can have downstream effects if the laser head catches on one of these pieces as it traverses during operation, moving or dragging it along. While some find it easiest to cut sheets from the roll and allow them to relax to a flat position before cutting, the most efficient way is to use air suction to hold the material flat. While not native on many laser models, some can be modified to have downward suction.
#4 - Utilize nozzle air assist
The materials, adhesives, solvents, dyes, and coatings used in nylon laminates produce a mixture of fine particles when cut. These can collect on the surface of the material, causing discoloration. This is especially noticeable on dark solid colors, like black, where the residue gives a shadow-like appearance around the cut. A properly positioned and tuned air assist (air flow through the nozzle, powered by an air pump or air compressor) will keep the particles flowing through the cut to the opposite side of the material, to be evacuated by the exhaust.
Alpen Design Works provides product development services, including product design and prototyping, production readiness, laser cutter training and consultations, and more. Contact Kory Brown at kory@alpendesignworks.com for more information.